Чёткие, скоординированные действия, выполняемые по заданному человеком алгоритму. Иногда кажется, что он живой и каждую операцию выполняет осознанно.
В начале декабря в литейном цехе жаропрочного литья лопаток турбин ПАО «ОДК — Сатурн» (входит в Объединённую двигателестроительную корпорацию Госкорпорации Ростех) запущена новая роботизированная линия по производству керамических форм с огнеупорной оболочкой. Журналист «Черёмухи» Ирина Рязанова посмотрела, как работает робот-манипулятор, и узнала, каков результат от внедрения новой линии.
Стальная рука плюс интеллект
«Бесконечно можно смотреть на три вещи: как горит огонь, как течёт вода и как другие работают». Эта ставшая крылатой шутка вспоминается, когда наблюдаешь за работой робота-манипулятора в литейном цехе № 41 «ОДК — Сатурн». Он не устаёт и не сбивается с заданного ритма, выполняет все действия с предельной точностью.
— Реализация проекта по оснащению нового литейного корпуса современным, лучшим в мире оборудованием происходит в чётко установленные сроки, хотя это и достаточно сложно в текущих условиях. Сказалась пандемия, программирование и управление запуском оборудования выполнялись удаленно за тысячи километров, но мы справились! — отметил главный инженер «ОДК — Сатурн» Игорь Ильин.
Робот-манипулятор размеренно и плавно перемещается вдоль рельсового пути. По одну сторону установлены три пескосыпа барабанного типа, по другую — баки с суспензией. Рабочая зона роботизированной линии обнесена по периметру защитным ограждением, все операции совершаются без участия и доступа в технологический процесс человека. Движения робота задаются программой: оператору остаётся лишь выполнять функции контроля.
Заготовка, закреплённая на конце «руки» — собранный модельный блок — то отправляется в бак с суспензией для дополнительного смачивания перед обсыпкой, то погружается в барабан, где её обсыпает электрокорунд. Рядом расположены зоны сушки. После того как заготовка пройдёт необходимый цикл выдержки в зоне с заданными параметрами температуры и влажности, воск, из которого она изготовлена, выпарят, а в образовавшуюся полость керамической формы зальют металл.
— Зона обсыпки состоит из трёх камер, в каждой — песок заданной фракции. Зона сушки обладает контролем параметров микроклимата. Это нужно для того, чтобы высыхание слоёв происходило равномерно, — рассказывает об устройстве линии технолог цеха № 41 Наталья Павлова. — Вне зоны установлены баки, где замешивается суспензия для обсыпки. Мы разрабатываем технологию нанесения слоёв, сушки — для каждого изделия требуются свои характеристики. Впоследствии требуется лишь контроль за ходом выполнения этих операций на линии.
Роботизированная линия сократила потребность в персонале: чтобы обеспечить работу такой установки, нужны два человека. При этом пропускная способность производственного участка повышается в три раза.
— Суспензия, которая формирует керамические слои, очень тяжёлая, так что вручную выполнять такие манипуляции сложно, — признаётся технолог. — Кроме того, требуется особый контроль за тем, как наносятся слои, прежде всего, первый — ведь именно он задаёт форму для будущего изделия. Робот выполнит все заданные программой операции, не допустит ошибок или случайного брака. Поэтому преимущества такого оборудования очевидны. На манипулятор можно закрепить сразу несколько блоков — до пяти штук одновременно, так что за счёт этого повышается и скорость производства. К тому же новая установка рассчитана на работу с более габаритными деталями.
По подсчётам специалистов за месяц здесь произведут до трёх тысяч керамических форм. Новая роботизированная линия обеспечивает нанесение огнеупорного покрытия на формы для сопловых и рабочих лопаток турбины, в том числе с увеличенными размерами.
— Производственный цикл изготовления керамической формы происходит непрерывно: на собранный модельный блок, слой за слоем, наносится специально замешанная и приготовленная масса-суспензия, каждый слой просушивается в специальных зонах сушки и только после этого наносится следующий. И так происходит до того момента, пока не будет сформирована нужная керамическая форма, с необходимым количеством слоёв. В автоматическом режиме на протяжении всего цикла интеллектуальной системой роботизированной линии непрерывно осуществляется контроль за такими параметрами, как скорость вращения баков с суспензией, глубина и время погружения блоков в баки, продолжительность времени нахождения форм на конвейере в специальных зонах сушки. Осуществляется контроль за количеством наносимых на модельный блок слоёв. Наша роботизированная линия позволяет получить соответствующую заданным параметрам керамическую форму. Впоследствии в неё будет залит расплавленный жаропрочный сплав для получения отливок лопаток газотурбинных двигателей, — объясняет заместитель начальника цеха № 41 по технической части Сергей Костромской.
Интеллектуальная система позволяет контролировать и регистрировать более 50-ти технологических параметров, что повышает качество изготавливаемых деталей.
Драйверы роботизации
Лопатка турбины — один из самых наукоёмких и сложных в изготовлении компонентов газотурбинных двигателей для авиации, морских судов и энергетики. Такую продукцию выпускают всего шесть стран. Год назад, в декабре 2019-го, на территории «ОДК — Сатурн» руководство Госкорпорации Ростех и ОДК открыли крупнейший в России корпус, предназначенный для изготовления лопаток турбины.
Участок нанесения керамической огнеупорной оболочки литейного цеха № 41 уже в момент открытия был технически оснащён современной роботизированной линией. В декабре 2020-го, в связи с расширением номенклатуры выпускаемых изделий, производственные мощности цеха были увеличены за счёт ввода в эксплуатацию ещё одной единицы высокотехнологичного оборудования — роботизированной линии нанесения керамического покрытия.
— Цех специализируется на двух видах литья: монокристаллическое литьё направленной кристаллизации и равноосное. Ранее, в связи с особенностью керамического покрытия, мы могли использовать только один вид литья, — рассказывает заместитель начальника цеха по производству Михаил Коптев. — Сейчас эти процессы происходят параллельно: одна линия выполняет один тип литья, вторая — другой.
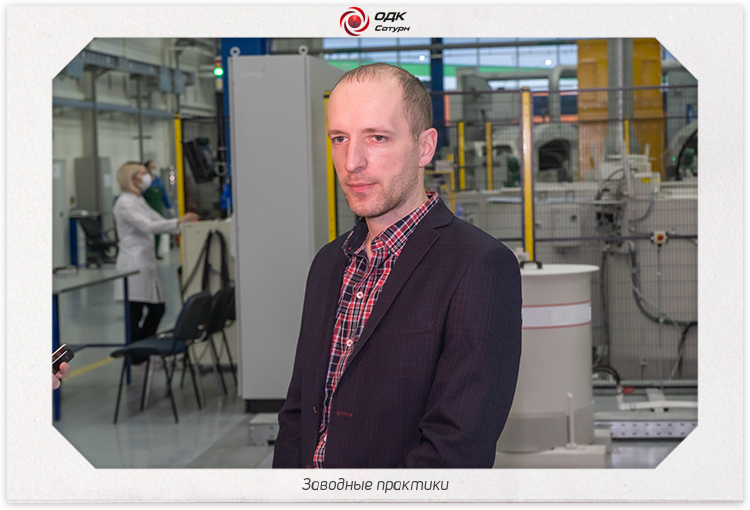
Метод отливки в керамические формы считается самым современным в литейном производстве. Его преимущество в том, что он даёт возможность создать точные формы, заданные в технологической документации. Автоматизированная линия исключает человеческий фактор, так что случайные погрешности практически полностью исключены.
Монокристаллические отливки и отливки направленной кристаллизации — уникальные изделия: лопатки, которые отливаются в таких формах, при постановке на двигатель способны выдерживать самые серьёзные нагрузки.
— Оборудование уникально тем, что в нём применяются новейшие технологии: лазерный уровень, контроллер суспензии баков. Робот может автоматически определять лучшие параметры блоков вне зависимости от их положения в зоне обсушки. За счёт того, что данная линия может работать с более габаритными блоками, мы расширяем ассортимент изделий отливки, — говорит Коптев.
Техническое и технологическое совершенствование цеха с установкой роботизированной линии не остановится. Скоро здесь появится цифровой рентгенографический комплекс установки для запрессовки воска.