Одна из важных задач руководителя компании — приложить максимум усилий, чтобы увеличить прибыльность предприятия, но при этом не допустить роста производственных затрат. В ПАО «ОДК — Сатурн» (входит в Объединённую двигателестроительную корпорацию Госкорпорации Ростех, является членом «Союза машиностроителей России») результата достигают в том числе с помощью методов и инструментов бережливого производства. В основе концепции — устранение всех видов потерь, экономически обоснованное использовании внутренних резервов, оптимизация бизнес-процессов. Журналист «Черёмухи» Ирина Рязанова узнала, как это работает. На конкретных примерах.
Учиться, чтобы работать
На «ОДК — Сатурн» часто говорят: «Пришёл работать — придётся учиться». Утверждение вполне обоснованное: на современном высокотехнологичном предприятии нужно постоянно обучаться новым техникам и технологиям, повышать квалификацию, осваивать соответствующие компетенции. Для того чтобы понять, чему и как учить, какие знания востребованы в настоящее время, работает управление развития.
— Мы в своё время приняли за основу проектный подход, смысл которого заключается в том, чтобы внедрять методы и инструменты бережливого производства через реализацию проектов по улучшению. Обучаем сотрудников — в последнее время с использованием дистанционных технологий. Впоследствии сотрудники будут реализовывать свои проекты уже непосредственно в тех производственных подразделениях, где работают. Мы им оказываем методологическую, консультационную помощь, — рассказывает начальник управления развития производственной системы «ОДК — Сатурн» Илья Клеймёнов.
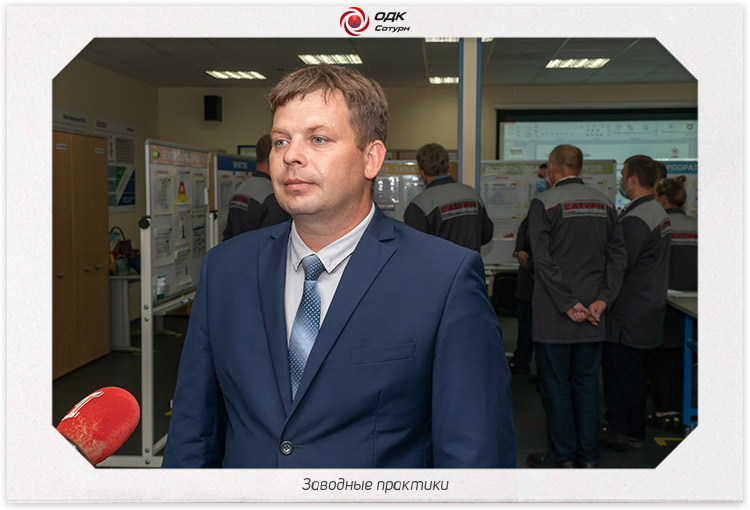
Специалисты утверждают: исходная точка любого развития — выявление проблем, противоречий, затруднений. В управлении развития занимаются поиском причин, которые вызывают сложности, а также решают, что нужно изменить для их устранения. Иногда достаточно провести мероприятия организационного характера, но бывают случаи, когда требуются вложения.
— На самом деле все проекты, которые предлагают наши сотрудники, важны и значимы. Есть те, которые на первый взгляд кажутся не слишком удачными, а на практике дают отличные результаты — исключаются вроде бы невидимые потери, упрощаются рутинные процессы, — говорит Клеймёнов. — Бывает, наоборот: в теории проект смотрится красиво, даже амбициозно, а на практике его воплощение тормозится: предлагаемые новшества сложны в плане организации или требуют дополнительных ресурсов, инвестиций.
Lean-технологии — термин, который пришёл из западноевропейской практики. Теория быстро прижилась в России, даже приняты ГОСТы по бережливому производству. На рыбинском предприятии вопросами повышения эффективности организации работы занимались ещё в советские годы.
Методы оптимизации труда применяли на моторостроительном заводе со второй половины ХХ века, во времена, когда предприятием руководил Павел Дерунов. Он предложил принципы научной организации труда (НОТ) в производстве. Идеи Дерунова получили одобрение на уровне руководства страны, после чего соответствующие отделы НОТ стали обязательным атрибутом советских предприятий. В 1971-м году Дерунову за эту разработку вручили Государственную премию СССР.
— Суть бережливого производства — выявление и устранение так называемых «узких» мест, потерь, которые не добавляют процессу ценности и значимости, — поясняет начальник управления развития производственной системы. — К таким потерям относятся, например, лишние перемещения персонала, ожидание обработки деталей, перепроизводство. Благодаря методам бережливого производства можно анализировать отдельно взятую ситуацию и выявить организационные недостатки. Бережливым можно сделать любой процесс: в офисе, на производстве, в логистике — где угодно. В конечном итоге все изменения направлены на то, чтобы повысить эффективность и прибыльность бизнеса.
Время — деньги
В бережливом производстве каждая мелочь играет особую роль, помогая довести производственный процесс до идеала. Так, зная, где какой инструмент или документ находится, в нужный момент его можно взять автоматически, не отвлекаясь на поиски — а это в итоге даёт экономию рабочего времени. То, как выглядит рабочее место — уже не индивидуальное решение, а закреплённый в документах порядок вещей.
Ещё пример: в одном из цехов привыкли складывать крупногабаритные приспособления для закрепления деталей на станке друг на друга. Для того чтобы взять нужную, приходилось заниматься переборкой, тратить на это время. В итоге изготовили простую конструкцию — ячейки для хранения, где каждое приспособление в своём отсеке.
— Некоторые результаты не видны мгновенно — они проявляются лишь со временем. Такие показатели называют условным эффектом. Ежегодно условный экономический эффект от реализации проектов по бережливому производству составляет примерно 17 — 20 миллионов рублей. Это не «живые» деньги, но вполне подтверждённый расчётами эффект, — утверждает Клеймёнов.
«ОДК — Сатурн» является разработчиком двух практик, признанных лучшими. Деятельность в области лидерства и проектного подхода выбраны для трансляции на других предприятиях «ОДК».
— Внедрение технологий бережливого производства «Сатурн» начал совместно с французским предприятием Safran в рамках изготовления двигателя SaM-146. На тот момент во Франции lean-технологии были уже широко известны. Остановились на проектном подходе, так как он позволяет систематизировать применение методов бережливого производства: в проектах есть этапы анализа, планирования, реализации. Программно-проектное управление на «Сатурне» применяется с 2009-го года: наработана нормативная документация, есть уже определённый опыт — поэтому данную практику признали наиболее успешной. Теперь этот опыт распространяется и на других предприятиях ОДК, — рассказывает Илья Клеймёнов.
Проект в области лидерства позволяет различать уровень подготовки специалистов в рамках бережливых технологий. Для этого ввели систему квалификационных поясов.
— Если специалист успешно завершил проект в качестве руководителя, набрал необходимый объём компетенций в области бережливого производства, то он получает квалификационную категорию «зелёный пояс». Можно и дальше развивать компетенции в области бережливого производства, беря полностью на себя ответственность за методологию в проекте, в том числе, становясь наставником для тех, кто хочет стать «зелёным поясом». Сопровождение не менее двух проектов в качестве ответственного консультанта, наличие необходимого уровня компетенций дают возможность претендовать на присвоение квалификационной категории «чёрный пояс», — объясняет Клеймёнов.
В настоящее время в «ОДК — Сатурн» трудятся около 30-ти обладателей «чёрных поясов» по бережливому производству.
Успеть за 60 секунд
«Фабрика процессов» — особое место на предприятии, где проходит обучение основам бережливого производства. В ходе учебно-имитационного тренинга сотрудники могут на практике применить полученные знания.
— Эффективнее один раз показать, в чём суть бережливых технологий, чем многократно в теории повторять об этом, — говорит главный метролог «ОДК — Сатурн» Дмитрий Барвинок о тренинге среди сотрудников этого подразделения. — Я рассматриваю данное мероприятие не просто как возможность обретения, закрепления значимых компетенций, но и как возможность командообразования. На тренинге мы учимся слушать друг друга, выстраивать командную работу, нацеленную на достижение общего результата.
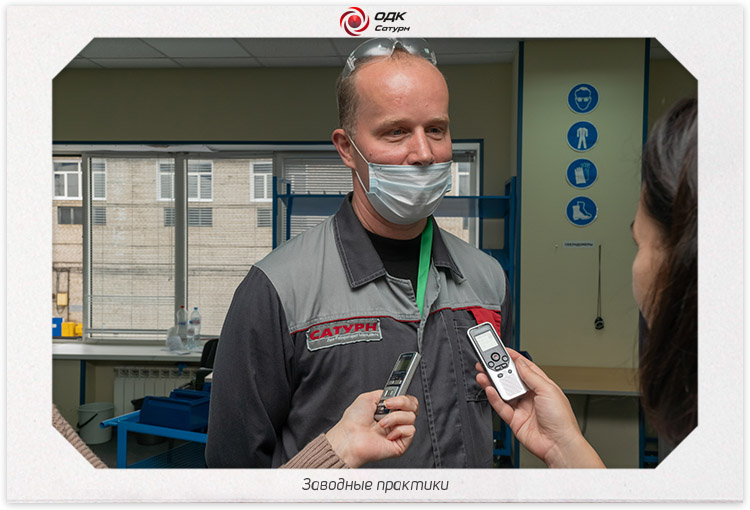
Под присмотром опытных тренеров происходит разбор, анализ сложившихся в ходе тренинга ситуаций. Это позволяет понять, как именно можно ускорить выполнение поставленной задачи, исключить потери во времени и лишние траты ресурсов, но в то же время не допустить снижения качества продукции.
— Обучение происходит в три этапа. Группа занимается условным «выпуском» конкретных деталей — бензонасосов. За двадцать минут — это время учебной «смены» — необходимо организовать процесс сборки таким образом, чтобы обеспечить бесперебойную работу с тактом выпуска один насос в минуту, — комментирует ведущий специалист управления развития производственной системы «ОДК — Сатурн» Николай Шумилов. — Сначала обучаемые работают, как могут, самостоятельно определяя функционал каждого участника. Здесь важно понять исходный уровень организации группы. Затем уже происходит усовершенствование трудового процесса за счёт устранения временных и организационных потерь.
После того, как отведённое на практику время завершится, группа под руководством тренеров приступает к анализу результатов. Важно понять, почему не удалось достичь заданных показателей, на каком этапе происходит потеря драгоценных секунд и что можно предпринять, чтобы ускорить работу без потери качества. В итоге такого обсуждения специалисты учатся самостоятельно находить слабые участки в технологических и организационных процессах, предлагать варианты по их устранению.
— На первом этапе группа собрала всего семь насосов. После разбора ошибок и принятия решений по оптимизации труда, выпуск увеличился вдвое. Потерь со стороны качества не было. После первой «смены» наши обучающиеся, например, отказались от одной из контрольных операций — функцию самоконтроля переложили на слесарей-сборщиков. Перед третьим раундом нужен более тщательный анализ ситуации, чтобы уже безошибочно выполнить производственную программу, — объясняет Шумилов.

По словам организаторов тренинга, обучение начинается с освоения системы 5S, которая включает в себя пять принципов: сортировку — устранение ненужного из рабочей зоны, создание порядка — удобное, рациональное размещение нужных в работе предметов, содержание в чистоте, стандартизацию — описание всех этапов по поддержанию порядка на рабочем месте и совершенствование — соблюдение установленных правил, их контроль и доработку с учётом изменения внешних факторов. Об успешном внедрении системы 5S после первого раунда свидетельствует значительное сокращение времени выполнения операции за счёт устранения потерь времени на поиск необходимых предметов и информации, а также сокращение запасов до минимальных, но достаточных.
— Учебно-имитационный тренинг «Фабрика процессов» проводится в «ОДК — Сатурн» с 2014-го года. Около 2.000 сотрудников предприятия прошли обучение, в планах — ежегодно обучать не менее 400 специалистов. Тренинг также проводится для представителей иных предприятий, входящих в ОДК, и других компаний,— говорит эксперт управления развития производственной системы «ОДК — Сатурн», обладатель «чёрного пояса» по бережливому производству Виктория Коршунова. — Зачастую для эффективной организации процесса даже не нужны дополнительные вложения, необходимо и достаточно выявить и устранить ненужные действия в цепочке создания ценности. Цель тренинга — не просто добиться требуемого объёма выпуска продукции за отведённое время «любой ценой», а так организовать процесс, чтобы участники могли сохранять требуемый ритм работы на протяжении длительного времени, превышающего длительность раунда. Это легко проконтролировать по итогу раунда с помощью системы показателей, которые отражают эффективность процесса с разных сторон: безопасности, качества, исполнения заказа, затрат и корпоративной культуры. Стабильность процесса является как результатом преобразований, так и отправной точкой для дальнейших улучшений.