Проектная деятельность в ПАО «ОДК — Сатурн» (входит в Объединённую двигателестроительную корпорацию Госкорпорации «Ростех») — это драйвер развития предприятия. Большими и малыми проектами специалисты постоянно улучшают работу подразделений компании. В новом выпуске «Заводных практик» рассказываем о проектах, которые помогли сделать ряд процессов в рамках деятельности ПАО «ОДК — Сатурн» более эффективными. Эти решения признали одними из лучших по итогам корпоративного конкурса ОДК.
Борьба за эффективность
Каждый год в рамках корпорации ОДК проходит конкурс проектов по развитию производственной системы. Реализованные практики рассматриваются в трёх номинациях: «Лучший производственный проект», «Лучший офисный проект» и «Лучший проект в области качества». Объединяет все направления использование инструментов бережливого производства, которые не просто помогают наладить работу на конкретном участке, но и могут тиражироваться на других предприятиях.
— Официально проектный подход на предприятии применяется с 2009-го года. Три года назад в ОДК впервые стартовал конкурс, целью которого стало выявление лучших практик по применению методов и инструментов «бережливого производства» и их распространение. Всего в 2019-м году на конкурс заявляли около 50-ти проектов, — говорит начальник управления развития производственной системы «ОДК — Сатурн» Илья Клеймёнов.
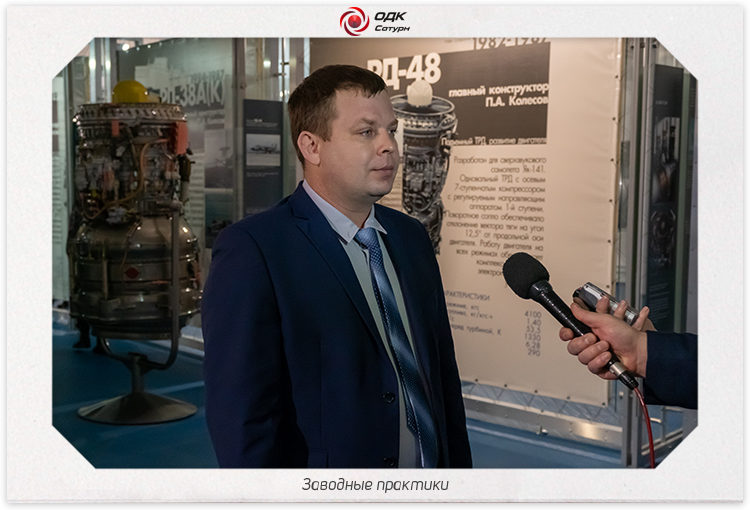
«ОДК — Сатурн» совместно с Ярославским региональным отделением «Союза машиностроителей России» представил на конкурс десять проектов. Экспертная комиссия Объединённой двигателестроительной корпорации после проведения заочного этапа выбрала проекты, вышедшие в финал. В итоге «Сатурн» занял призовые места во всех номинациях.
Главная идея — в том, чтобы вовлечь в процедуру совершенствования производственных процессов как можно больше сотрудников. Для решения той или иной задачи формируется команда специалистов. Причём разработка и внедрение новых методик, технологий в практику происходит без отрыва от основной работы.
— В рамках проекта мы определяем контрольные точки, в которых следует достичь определённого результата. Это оптимизация процессов производства, связанная с уменьшением потерь. Важно, чтобы по завершению проекта можно было измерить некие показатели, доказав эффективность предложенной системы. Условный экономический эффект от проектной деятельности за прошлый год составил примерно десять миллионов рублей — это связано с исключением потерь, лишних передвижений продукции, совершенствованием процесса документооборота, — поясняет Илья Клеймёнов. — На предприятии сейчас реализуется около 150-ти проектов, мы их отслеживаем, анализируем результаты. Лучшие практики будут рекомендованы к участию в корпоративном конкурсе 2020-го года.
Оптимизация без отрыва от производства
Основа бережливого производства — работа по сокращению и устранению потерь, и как следствие, издержек. Никто не заинтересован в том, чтобы детали долго лежали на складе, ожидая контрольных измерений. Как оптимизировать работу? Порой достаточно навести порядок в отделе, продумать систему поступления продукции и передачи её после контроля и измерений.
Обучать и развивать
Технический прогресс требует постоянного обучения персонала — появляются новые компетенции, методики работы, которые нужно освоить в кратчайшие сроки. Самостоятельная подготовка не всегда даёт требуемого результата, поэтому задача внедрения системы обучения персонала оказалась актуальной.
— Любой проект нацелен на оптимизацию как производства в целом, так и отдельных его элементов: повышается производительность, улучшаются условия труда, — рассуждает главный контролёр «ОДК — Сатурн» Валерий Гречин. — Наш проект был направлен на создание системы компетенций работников бюро технического контроля. Мы разработали новую инструкцию по управлению персоналом, продумали систему действий, которые способствуют поддержанию и развитию важных компетенций. В проекте мы разделили общие знания — ими должны обладать все сотрудники бюро технического контроля — и целевые, которые связаны с конкретной должностью.
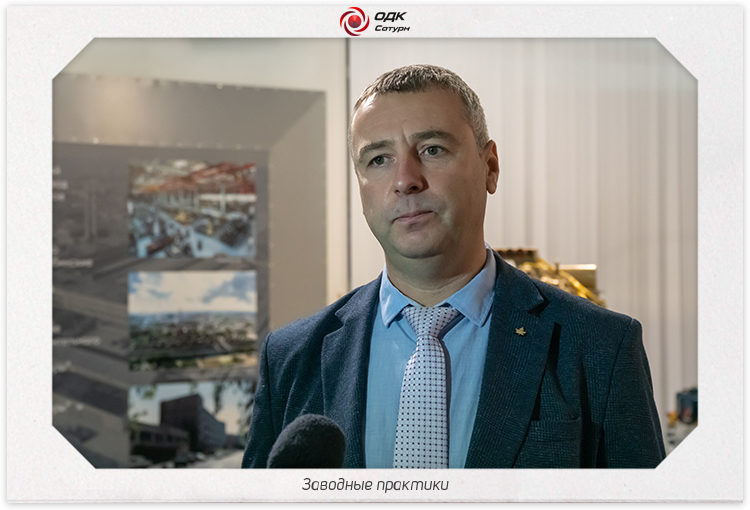
Систематизация работы по подготовке контролёров привела к тому, что теперь этот процесс не только занимает меньше времени, но и проходит на качественно ином уровне. Для каждого сотрудника определили набор профессиональных требований. Тестирование позволяет определить степень развития компетенций. Результаты помогают не только выявить сложности в овладении теми или иными процессами, но и способствуют карьерному росту самого работника.
Экономить время
Сборка двигателя — процесс технически сложный и ответственный. Кажется, ускорить его не в ущерб качеству работы практически невозможно. Но в ходе анализа каждой операции моторостроителям удалось определить, на каких этапах и по какой причине происходят потери по времени.
— В конкурсе проектов по развитию производственной системы ОДК участвовал в первый раз. Поэтому вдвойне приятно, что проект сразу отметили, присудили второе место. Перед нами поставили непростую задачу — сократить цикл сборки двигателя М70ФРУ-2. Аналогичных проектов, которые можно было бы рассмотреть в качестве примера, почерпнуть какие-то идеи, не было, — делится мастер производственной группы «Сборки изделий» Юрий Васильев. — Анализировали каждый этап работы, думали, где происходят потери времени и как их можно избежать.
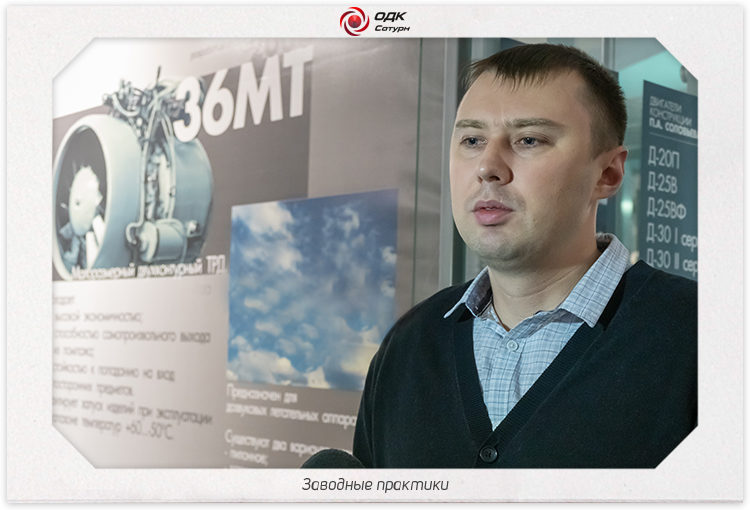
Поставленную задачу удалось решить с помощью современных методов: аддитивных технологий и компьютеризации. Особое внимание уделили организации рабочих мест. Заменили традиционные технологические карты и чертежи с планом сборки на компьютерные визуальные модели.
Слесарь-сборщик перед каждой операцией может просмотреть видеоролик с инструкцией, где детально показан процесс монтажа на определённом этапе.
— Такая визуализация облегчает восприятие информации. Суть работы может понять даже слесарь с невысоким квалификационным разрядом. Виртуальную модель узла, детали можно рассмотреть в разных плоскостях, наглядно увидеть, как происходит сборка. Дополнительно мы разработали альбомы визуализации монтажа трубопроводов — это цветные изображения, выполненные в объёме, которые показывают важные этапы сборки, — рассказывает Юрий Васильев. — В результате внедрения проекта удалось сократить время сборки двигателя с 14-ти дней до семи.
Оптимизировать документооборот
Рассмотрение любого документа требует времени: определить суть проблемы, предложенные варианты её устранения, подготовить грамотный ответ. Большая загрузка специалистов конструкторского отдела серийного сопровождения производства по рассмотрению входящих документов, таких как, разрешения на отклонения, разрешения на замену материала и карточек запроса на изменение конструкторской документации, а в связи с этим нехватка временных ресурсов на другие важные направления деятельности подразделения, стали предпосылкой следующего проекта.
— Рабочая группа в ходе изучения проблемы рассмотрела досконально весь этап формирования документации. Прежде всего, мы выявляли те стадии, которые безболезненно можно сократить, чтобы в целом ускорить документооборот. Пришли к выводу, что можем отказаться от дублирования электронных документов бумажными, — говорит заместитель начальника конструкторского отдела серийного сопровождения производства Иван Чепцов. — Команду проекта составили специалисты не только конструкторского отдела серийного сопровождения производства, но и службы главного конструктора по серийным двигателям Д-30 КУ/КП и производства — подразделений, с которыми в первую очередь взаимодействует конструкторский отдел и чьи предложения и интересы должны были учитываться при реализации проекта. В ходе совместной работы улучшения касались разных сфер деятельности подразделения, мы постоянно и плодотворно взаимодействовали со службой качества и службой по информационным технологиям. В итоге условный эффект от внедрения проекта — около шести миллионов рублей за 2018-й год. Это яркий пример того, насколько успешной может быть командная работа при решении производственных задач.
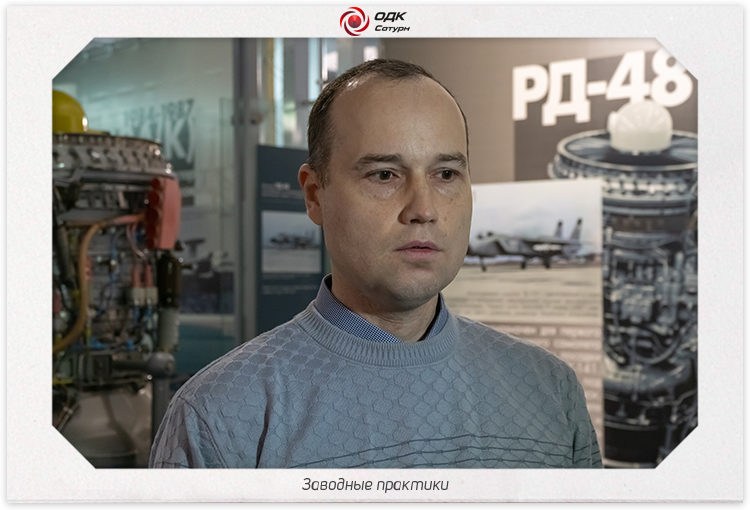
Навести порядок
Важность следующего проекта обусловлена тем, что объёмы производства по программе LEAP с каждым годом увеличиваются. Для соблюдения графика отгрузки готовой продукции используется новое современное оборудование и обеспечивается своевременный контроль продукции. Благодаря проведённой работе участники проекта смогли повысить пропускную способность участка за счёт исключения дублирующих контролей, перевода части операций на самоконтроль и сокращения потерь рабочего времени, без увеличения численности отдела. Это позволило своевременно выполнить весь необходимый объем контроля в рамках программы LEAP на 2018-2019 годы.
В отделе технического контроля цеха № 34 занимаются проверкой качества изготовленных лопаток. Детали поступают постоянно — раньше их складывали в специальный ящик, откуда контролёры забирали их на проверку в случайном порядке.
— Сейчас мы продумали организацию зон хранения для деталей, куда они поступают до и после проверки. На специальных стеллажах размечены полки. С одной стороны, контролёры видят объём работы и понимают очерёдность, в которой её следует выполнять. С другой стороны, мастера могут самостоятельно забрать годные детали в работу. В итоге возросла поточность производства, — объясняет суть изменений начальник отдела технического контроля цеха № 34 Евгений Мясоедов.
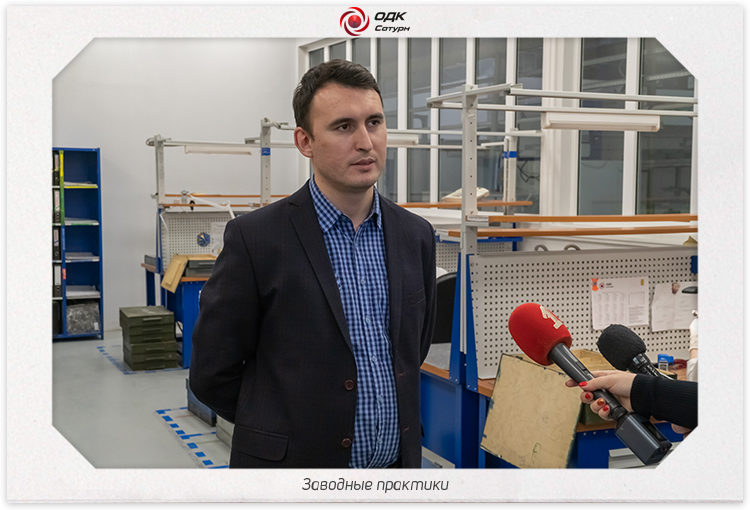
Результаты внедрения новой системы организации приёма деталей и последующей их отправки в производство вполне ощутимы: за прошлый год контролёры проверили 80.000 деталей, что вдвое больше, чем за 2018-й. В планах — дальнейшая оптимизация работы.
— Важно, что увеличив пропускную способность участка контроля, штат контролёров остался прежним: сократили время на поиск инструментов, исключили лишние операции при контроле, оптимизировали процесс приёма и передачи деталей, — говорит Евгений Мясоедов. — Участие в проекте помогло ускорить этот процесс, провести «мозговой штурм», проанализировать каждый этап работы и выявить «слабые» места.
Улучшить качество
В ходе реализации ещё одного проекта удалось достичь значимых результатов по улучшению качества изготовления лопаток в кузнечно-прессовом корпусе № 2.
— За счёт эффективной работы команды проекта удалось увеличить выход годных деталей на 15 %, — говорит заместитель начальника корпуса № 2 по технологической части Антон Опахин. — Мы работали над оптимизацией процесса выдавливания, над обеспечением стабильности размеров заготовок после выдавливания, над стандартизацией правил настройки оборудования и штамповой оснастки, над визуализацией на рабочем месте. Большое внимание уделили стандартизации процесса доводки штамповой оснастки, внедрению технологических усовершенствований процесса штамповки. Результаты изготовления партий лопаток в 2019-м году подтвердили достижение всех ключевых показателей проекта, а трансляция внедрённых мероприятий на однотипные лопатки позволяет повысить качество их изготовления.
По мнению участников корпоративного конкурса проектов по развитию производственной системы ОДК, участие в подобных конкурсах мотивирует к улучшению производственных процессов за счёт внедрения методов и инструментов «бережливого производства», позволяет предприятиям корпорации обмениваться опытом, а победы вдохновляют специалистов на новые идеи.