Девятнадцатого июля в Москве на IV Евразийском аэрокосмическом конгрессе состоялось вручение премий «Авиастроитель года». Церемония награждения лауреатов и дипломантов по итогам 2019-го года — часть деловой программы форума МАКС-2021. ПАО «ОДК — Сатурн» (входит в Объединённую двигателестроительную корпорацию Ростеха) отметили сразу в двух номинациях. О том, какие разработки рыбинских моторостроителей получили признание экспертного совета престижного конкурса — в свежем материале рубрики «Заводные практики».
Награды «Авиастроителя»
Конкурс «Авиастроитель года» проводится с 2011-го. Ежегодно экспертный совет рассматривает множество уникальных работ от ведущих специалистов авиационной промышленности. Наиболее актуальные, инновационные проекты и разработки отмечают наградами. Торжественную церемонию в этом году организовали в рамках деловой программы Международного авиационно-космического салона — 2021.
Лауреат в номинации «Лучший инновационный проект» и дипломант «За создание новой технологии» конкурса «Авиастроитель года» — «ОДК — Сатурн» — вновь подтвердил статус передового высокотехнологичного предприятия.
Первую награду рыбинские моторостроители получили за создание инновационного литейного производства, вторую — за разработку безрениевого высокожаропрочного никелевого сплава.
— Создание инновационного литейного производства позволило ОДК стать лидером в Российской Федерации по изготовлению отливок лопаток газотурбинных двигателей различного назначения. Проект увеличивает долю выпуска гражданской продукции в продуктовом портфеле, формирует важное направление коммерческого развития предприятия, — отмечает заместитель генерального директора — управляющий директор «ОДК — Сатурн» Виктор Поляков. — Второй проект — материаловедческий, не свойственный нашей деятельности. Но, являясь разработчиком перспективных двигателей, мы понимаем: там, где есть конструкторские бюро, должны быть новые перспективные технологии и материалы, поэтому мы взялись за это направление. Используя нашу уникальную техническую и исследовательскую базу, смогли получить достойный результат.
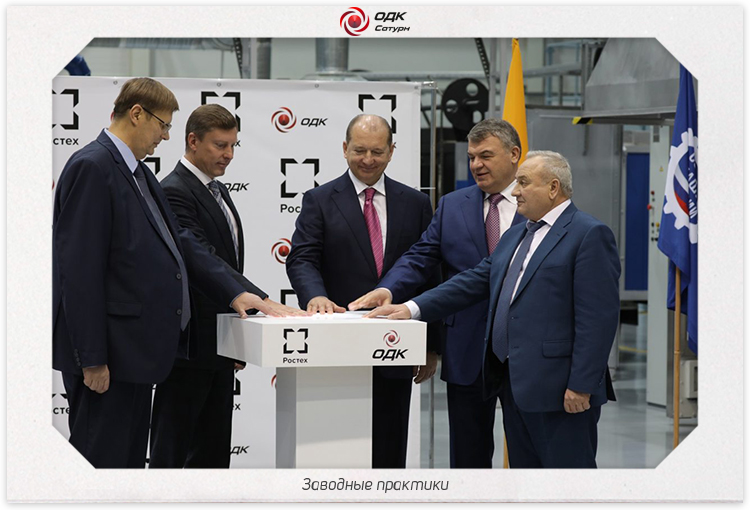
В «ОДК — Сатурн» понимают: постоянное совершенствование и развитие технологий — это вклад в повышение конкурентоспособности собственной продукции. Благодаря поддержке Объединённой двигателестроительной корпорации, правительства Ярославской области реализации федеральных целевых программ, формируется новый облик предприятия, на базе которого за счёт вложений в основной капитал создаётся высокотехнологичное производство и испытательные комплексы. За последние годы на предприятии выстроена эффективная производственная система планирования и учёта, выработаны показатели оценки деятельности производственных подразделений, внедрены мотивационные механизмы, нацеленные на повышение выработки и снижение производственных затрат.
Новый литейный
Новый литейный комплекс по изготовлению турбинных лопаток — гордость «ОДК — Сатурн». Сюда приводят гостей предприятия: от школьников, которые только начинают знакомиться с производством, выбирая профессию, до чиновников федерального уровня и иностранных коллег. Широкие коридоры, светлые цеха с современным оборудованием, автоматизированные линии, роботизированные комплексы. Все технические решения направлены на удовлетворение высоких требований к литым заготовкам. Новое литейное производство уже имеет сертификаты соответствия международным стандартам.
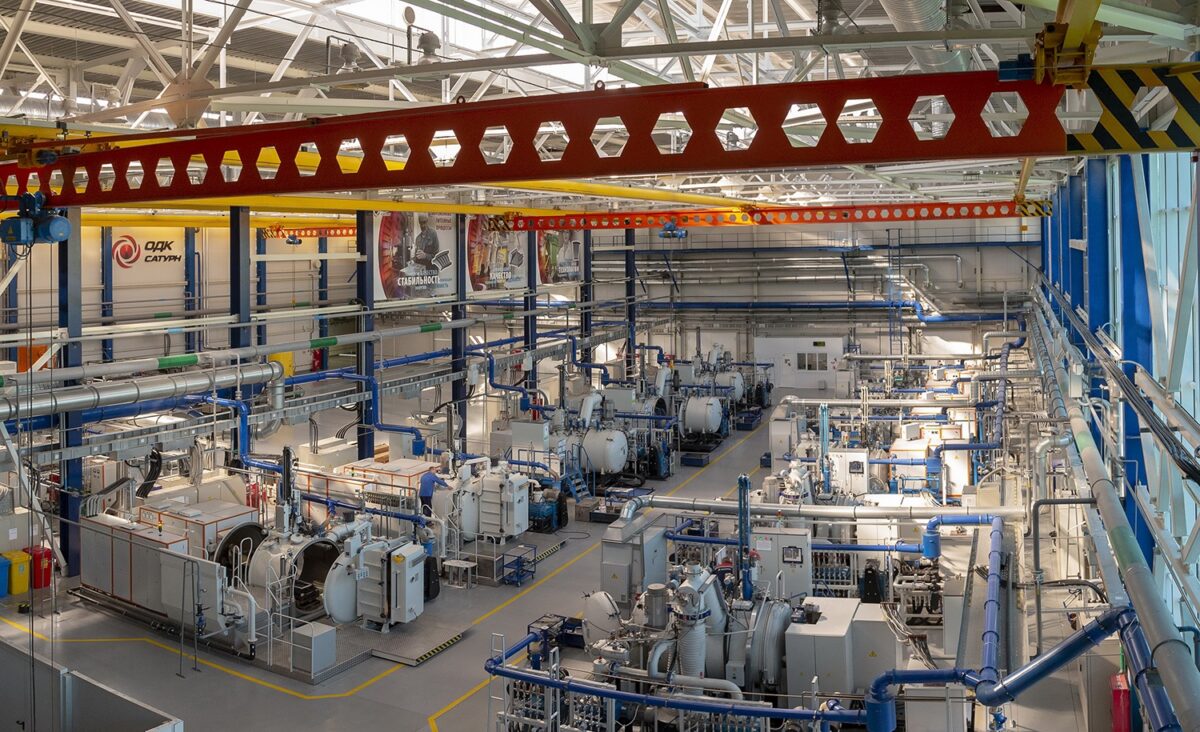
Лопатка турбины — один из самых наукоёмких и сложных в изготовлении компонентов газотурбинных двигателей для авиации, морских судов, энергетики.
— Такую продукцию производят только шесть стран в мире, она требует сложнейших расчётов при проектировании и очень высокой точности в изготовлении. Проект, без преувеличения, выводит российское двигателестроение на новый уровень и позволяет претендовать на лидирующие позиции в этом высокотехнологичном сегменте, — цитировало ТАСС в декабре 2019-го первого замгендиректора Ростеха Владимира Артякова.
На производстве реализован полный цикл изготовления различными способами точного литья. Инновационная технология позволяет методом монокристаллического литья в керамические формы по выплавляемым моделям производить отливки рабочих лопаток газотурбинных двигателей с жёсткими геометрическими допусками до 0,05 миллиметров. При этом последующая механическая обработка практически не требуется. Плавильный участок оборудован печами отечественного производства, которые позволяют производить плавку и заливку при температуре до 1800 градусов Цельсия — это открыло возможность для применения новых жаропрочных материалов.
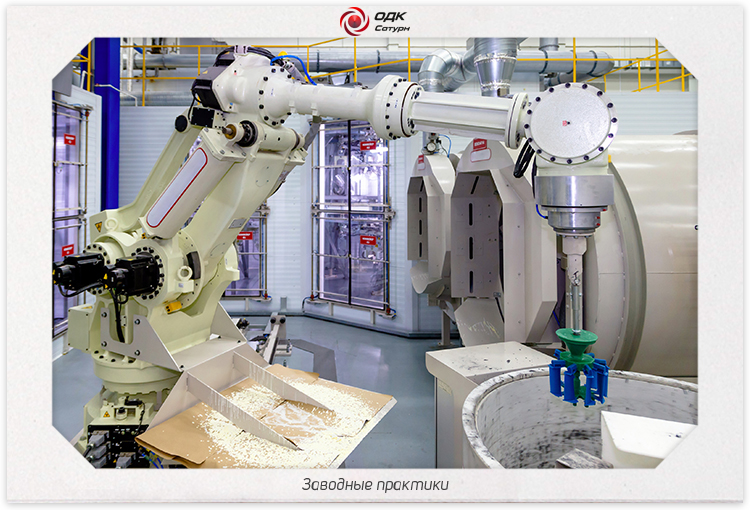
В отличие от традиционных литейных предприятий, в новом производстве применили экологически безопасные технологии: литейные установки не излучают тепло за счёт применения системы сбора и осаждения выделяемых паров масла. Вредные вещества не поступают ни в рабочую зону, ни в окружающую среду. Охлаждение технологического оборудования осуществляется от локальной станции оборотного водоснабжения цеха. В корпусе применили автоматизированный комплекс флуоресцентного контроля с замкнутой системой водоподготовки и локальными очистными сооружениями. В вытяжной вентиляции корпуса предусмотрены фильтры с максимальной эффективностью очистки.
Вместе с новым литейным комплексом развивается и последующая механическая обработка лопаток — специальные процессы наплавки, покрытий и лазерно-эрозионной обработки. Все это позволяет лопаточному производству «ОДК — Сатурн» соответствовать современным потребностям предприятий авиационного двигателестроения страны и международной кооперации.
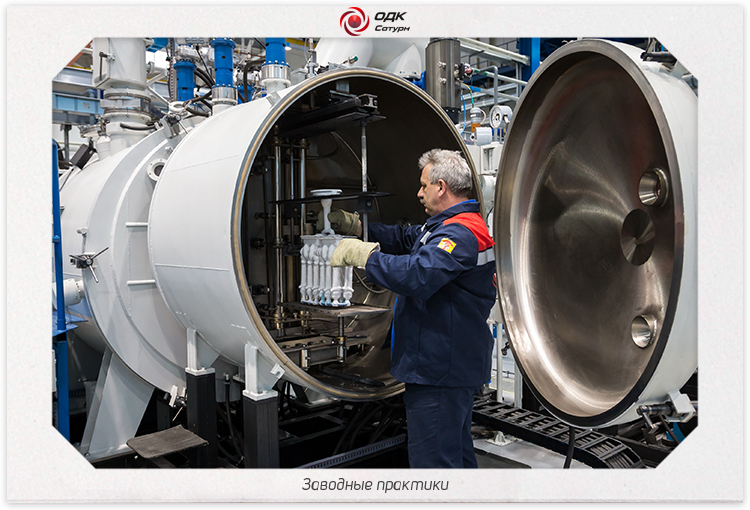
Новый жаропрочный
Проект по разработке нового безрениевого высокожаропрочного никелевого сплава для монокристаллических лопаток турбин длился три года. В течение этого времени специалисты проводили научные изыскания, подбирали оптимальный состав, отрабатывали технологии полного цикла изготовления деталей, проводили необходимые испытания образцов. Важно было получить такой материал, который содержал бы тугоплавкие элементы, способные выдерживать экстремально высокие температуры, и в то же время были бы приемлемыми по стоимости. Что касается температур — планка в двигателестроении только поднимается: ведь чем выше рабочие температуры двигателя, тем выше его КПД.
Уровень температурной работоспособности никелевых жаропрочных сплавов во многом определяется содержанием в них таких тугоплавких элементов, как вольфрам, молибден, ниобий, тантал, рений и рутений. При этом рений — крайне дефицитный элемент, в России его месторождения отсутствуют, а по стоимости он сопоставим с золотом. Рутений ещё более дорогой элемент, так как относится к платиновой подгруппе. Несмотря на выдающиеся характеристики жаропрочности сплавы, легированные рутением, не нашли широкого применения из-за высокой стоимости. Первым отечественным жаропрочным монокристаллическим сплавом, легированным рением, является ЖС32. Он используется почти во всех отечественных двигателях.
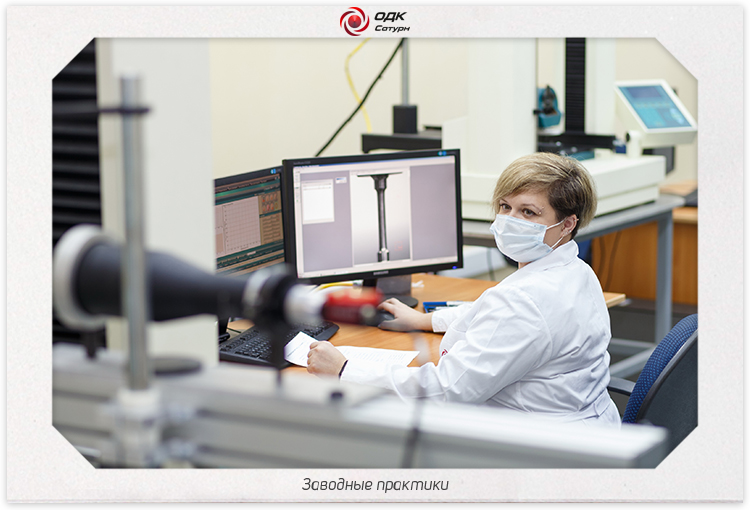
Разработчики смогли рассчитать и смоделировать химический состав нового сплава — СЛЖС32 — для замены ЖС32 без использования дорогостоящих редкоземельных металлов рения и рутения, что снизило стоимость его легирующих элементов в 3,5 раза. Благодаря применению математического моделирования и программных средств оптимизации удалось улучшить эксплуатационные характеристики сплава. Свойства нового материала позволяют применять его в более широком интервале температур и повысить коэффициент полезного действия газотурбинного двигателя. Новый сплав разработан, запатентован и готов к паспортизации.
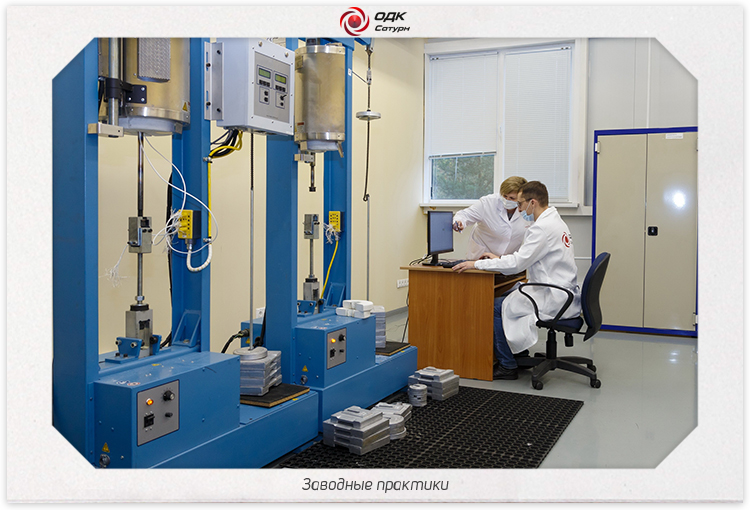
Специалисты рыбинского предприятия не только разработали новый материал, но и освоили полную промышленную технологическую цепочку от производства сплава до изготовления монокристаллических лопаток турбин высокого давления с его применением.
Новый сплав СЛЖС32 обеспечит повышение конкурентоспособности как существующих образцов двигателей, так и вновь разрабатываемых изделий.