Аддитивные технологии — одно из самых перспективных направлений развития производства во всём мире. Печать на 3D-принтере и в специальных установках позволяет получить нужную деталь за несколько часов, тогда как на её производство традиционным способом, включая создание формы для литья, ушло бы до двух месяцев. В отличие от механической обработки, технология аддитивной печати производит деталь не путём удаления лишнего материала из заготовки, а его наложением слой за слоем.
Несколько лет назад для российской промышленности аддитивные технологии были чем-то за гранью понимания. Единичные компании запускали дорогостоящие эксперименты, чтобы разобраться в их особенностях и просчитать выгоду от внедрения. Среди них был и рыбинский «ОДК — Сатурн». Сегодня компания практически завершила стадию эксперимента и можно говорить о том, что «выращенные» из полимерных композитных материалов детали постепенно становятся частью серийного производства.
На профильной секции V Международного технологического форума заместитель главного инженера опытного завода «Сатурна» Денис Федосеев отметил, что только в конструкции наземных двигателей для энергетических установок в 2017-м году установили более полутора тысяч деталей, изготовленных по аддитивным технологиям.
Таким образом, АТ на рыбинском производстве уже реальность. Руководитель проекта «Цифровая экономика» компании «ОДК — Сатурн» Павел Бехер констатировал, что основная задача аддитивных технологий — сокращение цикла подготовки детали — блестяще выполняется. И это значительно влияет и на технологию производства, и на конечную цену продукта.
— Стоимость деталей, которые мы получаем с помощью аддитивных технологий, не зависит от той партии, которая требуется нашему заказчику. А для механообработки это традиционное ограничение: чем больше партия, тем дешевле каждый экземпляр. Аддитивные технологии позволяют делать детали даже штучно. При этом их качество всегда будет на высоте, — подчеркнул Бехер, рассказывая об опыте рыбинских моторостроителей.
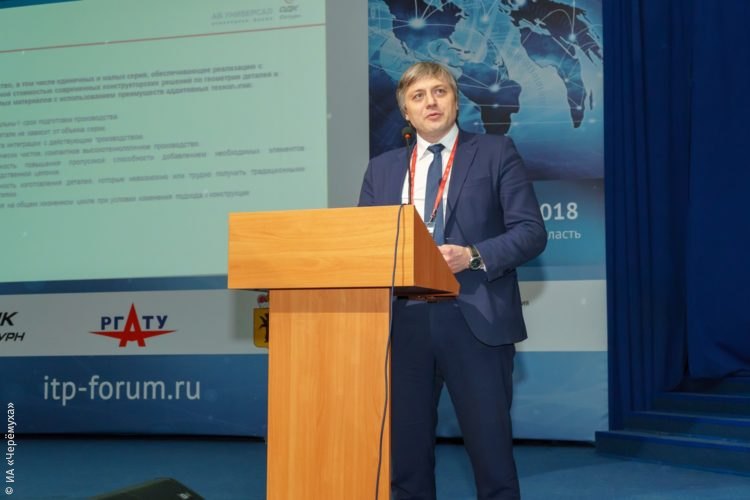
Сегодня «ОДК — Сатурн» наладило необходимый контроль на всех участках производства, начиная от проверки металлопорошковых композиций до контроля аддитивной детали, финальной геометрии и всех необходимых свойств, полученных на постобработке. В планах сформировать для каждой партии электронное досье с сохранёнными параметрами изготовления детали, которое заказчик будет получать вместе с готовой продукцией.
Заместитель генерального конструктора ОДК Дмитрий Карелин констатировал, что дискуссия об аддитивных технологиях от абстрактных рассуждений и надежд перешла в практическую плоскость.
— Сегодня мы видим нормальную производственную деятельность в области АТ. Теперь стоит вопрос, как сделать её более эффективной на этом этапе развития, — говорит Карелин. — В мире есть промышленно освоенные технологии, и есть инновационные аддитивные технологии, которые позволяют в разы увеличить скорость «выращивания» деталей. Мы должны быть в курсе этих технологий, развивать их, привлекать на этапе создания как можно больше малых компаний, институтов — создавать вокруг себя экосистему, которая позволила бы очень быстро от идеи до промышленной реализации осваивать эти новые технологические процессы.
— Изменений достаточно много. Большое количество деталей уже изготавливаются посредством аддитивных технологий и внедряются в серийные двигатели, выпускаемые «Сатурном», — говорит заместитель главного инженера опытного завода Денис Федосеев. — Перспективы мы оцениваем как очень положительные. Разрабатываются и получают паспорта отечественные материалы, порошковые композиции для аддитивной печати. К концу этого года мы планируем получить паспорт на отечественные титановый сплав, кобальтовый суперсплав, нержавеющую сталь. Это позволит внедрять детали в ещё больший спектр продукции.
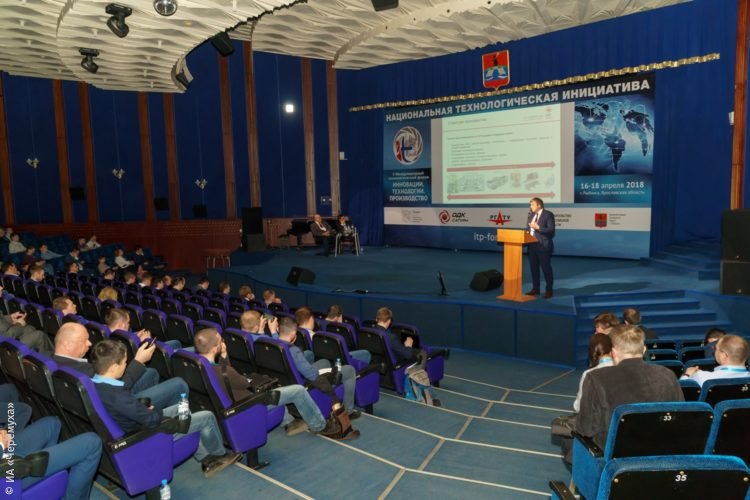
Аддитивные технологии полностью меняют облик предприятия. В первой части секции своим впечатляющим опытом внедрения АТ поделились представители зарубежных компаний General Electric, SLM Solutions, EOS и Siemens. Их доклады наглядно демонстрировали все возможности прорывной технологии и вызвали в зале большое оживление.
В ходе работы секции участники дискуссии обсудили последние тенденции в так называемой «Индустрии 4.0». Почему 4.0? Это синоним четвертой промышленной революции, которую знаменует массовое внедрение цифровых технологий в производство. Можете представить мозг всего завода в одном компьютере? Специалисты сходятся, что это может произойти в ближайшие два десятилетия. Например, технология цифрового двойника уже используется рядом крупнейших мировых предприятий, таких как General Electric, и осваивается на российских производствах. О своём опыте создания виртуальной модели производственной системы рассказала представитель компании «Би Питрон СП» Наталия Демкович.
— Мы построили трёхуровневую компьютерную модель промышленного предприятия, описывающую его с разной степенью детализации от формы и материалов заготовок до учёта складских помещений. С одной и той же моделью работают разные специалисты, которые могут, как получать, так и добавлять информацию, — объяснила Демкович.
Это дало возможность собирать и аккумулировать данные со всего производства и значительно сократить процент брака. Такие системы помогают выявить возможные неполадки в работе предприятия задолго до их появления.
Четвёртая промышленная революция постепенно уносит в прошлое такие понятия как чертёж и опытный образец. Их место занимают цифровые двойники и электронные модели.
О бесчертёжных технологиях в работе ГК «ПЛМ Урал» рассказал ведущий инженер компании по PLM-решениям Максим Конев:
— Современное программное оборудование позволяет полностью реализовать технологию без чертежей от конструирования до производства деталей. Вся информация заносится в 3D-модель изделия.
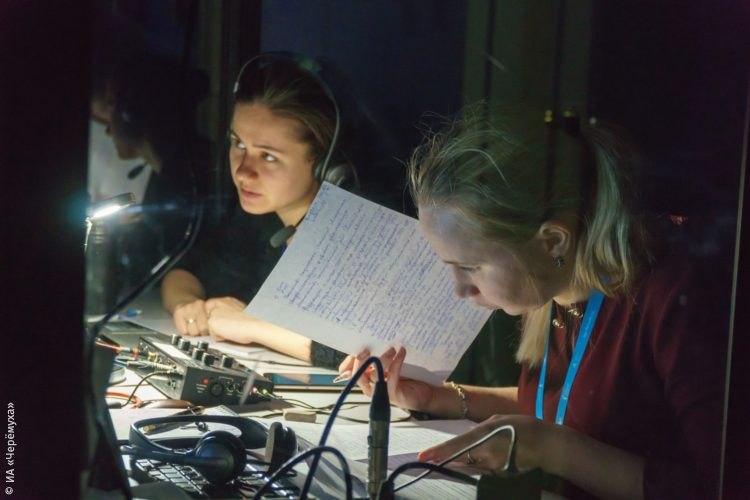
Но из-за отсутствия стандартов такие технологии внедряются на российских предприятиях достаточно медленно. Пока преобладает смешанная модель, когда электронное моделирование подкрепляется традиционным. Но в скором времени, уверен Конев, нас ждет полный отказ от бумажного документооборота.
Представитель японской компании Mazak Антон Петракович показал видео с производства и объяснил, как предприятие объединило станки в единое цифровое пространство, что позволило сократить время обработки деталей и диагностировать возможные поломки оборудования ещё до их появления.
Роботизированные производственные ячейки компании могут работать около 720-ти часов в месяц вообще без участия человека. Информация от каждой такой ячейки, которые связаны в единую информационную систему, позволяет анализировать данные о производительности всего завода.
Представитель Mazak уверен, что в недалёком будущем скачивание программ для станков станет таким же доступным, как сейчас приложений для смартфона.
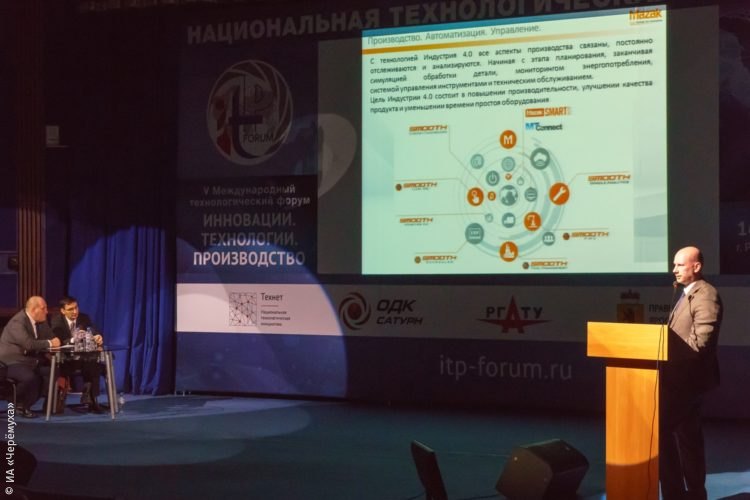
Доклады участников сессии доказывают, что производство меняется со стремительной скоростью прямо на глазах. Промышленность действительно стоит на пороге новой технологической революции. В такое время обмен опытом особенно важен, считают участники рыбинского форума.
— Например, в металлургии аддитивные технологии ещё только развиваются, — говорит представитель Машиностроительного центра «ССМ-Тяжмаш» «Северстали» Наталия Замиралова. — Мы обучаемся на опыте других предприятий и видим перспективы применения этих технологий у нас на производстве. На форуме мы познакомились со всеми будущими своими партнёрами, наладили производственные связи. Для нас важно, что форум проходит в России, при этом здесь собрались все основные пользователи аддитивных технологий. Нам это очень удобно, мы бы не смогли отправить такую большую команду от предприятия в зарубежную командировку.