Рыбинские моторостроители уже давно научились «выращивать» детали. Но чтобы «огород» давал более богатый «урожай», нужно выводить новые «семена» и разрабатывать более эффективные «удобрения». Так же и в аддитивном производстве — для изготовления деталей, отвечающих актуальным требованиям, важно иметь соответствующие материалы и отработанные технологические параметры процесса. В декабре прошлого года ПАО «ОДК — Сатурн» (входит в Объединённую двигателестроительную корпорацию Госкорпорации Ростех) получило паспорт на новые металлопорошковые композиции собственной разработки для аддитивного производства изделий морской тематики. О том, как ведётся исследовательская работа по получению нужных материалов и каким образом они применяются на практике — узнала Ирина Рязанова.
Синтез материалов. Синтез технологий
Центр аддитивных технологий «ОДК — Сатурн» — своеобразная площадка для научных исследований и экспериментов. В конце прошлого года специалисты головной материаловедческой организации — Центрального научно-исследовательского института «Прометей» в Санкт-Петербурге — приняли положительное решение о пригодности к использованию синтезированных материалов из кобальтового сплава и стали, разработанных «ОДК — Сатурн». Новый материал будут использовать в морских газотурбинных двигателях и судостроительной отрасли в целом.
— Заключения экспертов головной организации по материалам в судостроении свидетельствуют о том, что данные отечественные сплавы, синтезируемые из металлопорошковых композиций разработки «ОДК — Сатурн», по ряду характеристик превосходят уровень импортных аналогов, а также традиционно применяемых отечественных материалов, ранее разрешённых к применению в газотурбинных двигателях морского назначения. Безусловно — это ещё один большой шаг ОДК в развитии и внедрении аддитивных технологий в России, — отметил заместитель главного инженера опытного завода по аддитивным технологиям «ОДК — Сатурн» — руководитель проекта «Аддитивные технологии» в АО «ОДК» Денис Федосеев.
Разработка новых материалов — процесс хоть и не свойственный для «Сатурна», но абсолютно необходимый.
— У нас уже наработаны компетенции в сфере применения аддитивных технологий. Важно, что «Сатурн» является головным центром газотурбостроения для морского применения в России. Это даёт нам возможности понять, как ведут себя те или иные материалы в конструкции двигателя. То есть мы можем как ставить задачи по разработке материалов перед головной материаловедческой организацией, так и непосредственно влиять самостоятельно на выбор материалов, задавая набор требуемых свойств. Поэтому задачи, связанные с разработками новых материалов для нас актуальны, — объясняет главный инженер опытного завода «ОДК — Сатурн» Сергей Заводов.
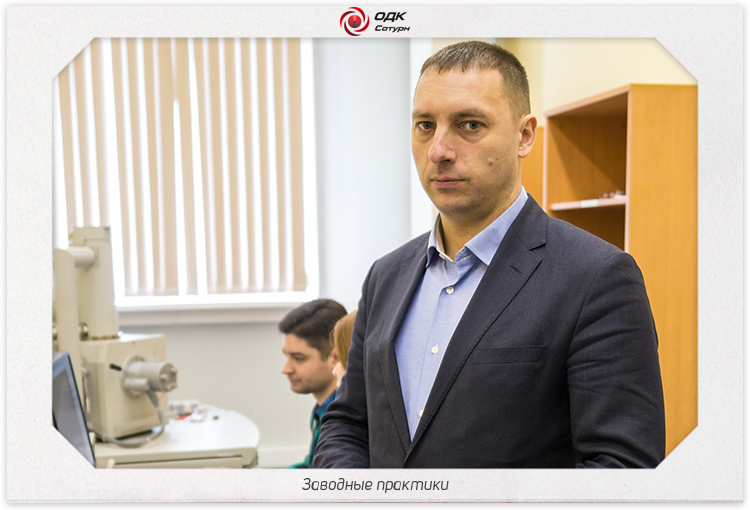
Три года назад, в конце 2017-го, в «ОДК — Сатурн» состоялись квалификационные испытания нового морского газотурбинного двигателя М70ФРУ-Р. Около 3 % деталей этого двигателя изготовили аддитивным способом. Тогда всерьёз заговорили о внедрении аддитивных технологий в конструкцию изделия. Но на тот момент для «выращивания» использовали импортные материалы: отечественных аналогов просто не было.
— Металлопорошковые композиции разрабатывали изначально для применения в авиационном производстве. Тогда провели паспортизацию в ВИАМ, а потом их валидировали для применения в морском двигателестроении, подтвердив стойкость к высокотемпературной солевой коррозии, — говорит Заводов. — Аналоги нового материала с точки зрения классической металлургии, конечно, имеются: в современных условиях обнаружить принципиально новый, инновационный материал довольно затруднительно. Важно то, что этот синтезируемый материал из металлопорошковой композиции адаптирован именно для аддитивного производства.
Процесс паспортизации нового материала — это комплекс исследований и испытаний, которые подтверждают возможность его использования в машиностроении. Главная цель — выявить недостатки ещё на стадии разработки. Свойства новых материалов изучают с помощью многократных разнообразных опытов и экспериментов, которые позволяют определить точный состав, прочностные характеристики, степень устойчивости к образованию трещин, стойкость к коррозии, технологические характеристики и многое другое. Полученные результаты формируют паспорт материала.
На основании паспортов создаётся перечень-ограничитель материалов, которые допускаются к использованию в двигателестроении.
— На данный момент мы имеем паспорта на три материала, разработанных в «ОДК — Сатурн». Ещё одна разработка находится в стадии подготовки паспорта. Материалы разные по характеристикам: титановый сплав — для деталей, которые не несут большой температурной нагрузки. Для более высоких температур — нержавеющая сталь и сплавы на основе кобальта, — говорит главный инженер опытного завода. — Наши материалы — первые в России для аддитивного производства, которые были внесены в перечень-ограничитель, и имеют допуск к использованию для изготовления деталей морских турбин.
Исследовательские работы на «Сатурне» по получению новых материалов будут продолжаться и в будущем. По словам специалистов, есть немалый интерес к сплавам на основе никеля — их применяют в турбинах высокого и низкого давления.
Складываем, не вычитаем
Принцип аддитивного производства заключается в том, что для создания детали сложной формы материал наносится последовательно слой за слоем, поэтому его расходуется столько, сколько нужно. То есть суть аддитивных технологий в сложении, без вычитания. Процессом управляет компьютер, в чьей памяти заложена трёхмерная модель будущей детали, нарезанная на тонкие слои-сечения. Толщина такого слоя, как правило, от 20-ти до 50-ти микрон. Для того чтобы «вырастить» деталь, выкладываются десятки тысяч слоёв. В итоге получается монолитная деталь с заданной внутренней и внешней геометрией. Скорость «выращивания» зависит от габаритных размеров деталей, геометрии, толщины стенок и варьируется от нескольких часов до нескольких дней.
— Центр аддитивных технологий «ОДК — Сатурн» располагает оборудованием для синтеза деталей как из полимерных, так и из металлических материалов, на текущий момент, позволяющим «выращивать» детали газотурбинных двигателей с максимальными габаритными размерами 400x400x400 миллиметров. Для аддитивного производства — это довольно большие размеры — показывает оборудование Центра Сергей Заводов.
Новое оборудование послойного сплавления металлических порошков поступило на предприятие в прошлом году. Установки позволяют ускорить технологическую подготовку производства деталей. Кроме того, полученные образцы легко изменить, откорректировать — в соответствие с замыслом конструкторов.
Время изготовления детали — основное преимущество, которым обладают аддитивные технологии.
Когда перед моторостроителями стояла задача производства спрямляющего аппарата перспективного гражданского авиационного двигателя, изначально планировали использовать литьё. Получилось, что цикл проектирования, изготовления преформ, разработки самой технологии займёт от девяти месяцев до года. Специалисты по аддитивным технологиям первую опытную деталь получили через неделю. И уже через месяц в цех механической обработки поступил комплект деталей нужного качества.
Предприятие внедряет аддитивные технологии в производство деталей камер сгорания, элементов внешней обвязки авиационных, морских и энергетических газотурбинных двигателей. Немалую долю в общем объёме аддитивного производства занимают детали и сборочные единицы испытательных стендов, приспособлений и специальных инструментов. Детали, полученные аддитивным способом, присутствуют в каждом новом двигателе, разрабатываемом «ОДК — Сатурн».